For some standard applications, incorporating fillers, colors, and other additives into a resin can be as easy as pre-blending all the ingredients together and loading them into a single-screw extruder hopper for strand pelletizing. As requirements become more stringent, the compounding process becomes more interesting, involved, and specialized.
Many types of compounding machines and mixers are available, and satisfactory compounds can be produced on most of them. While individual operator preference plays a major role, certain machines are more flexible and do a better job than others on specific compounds.
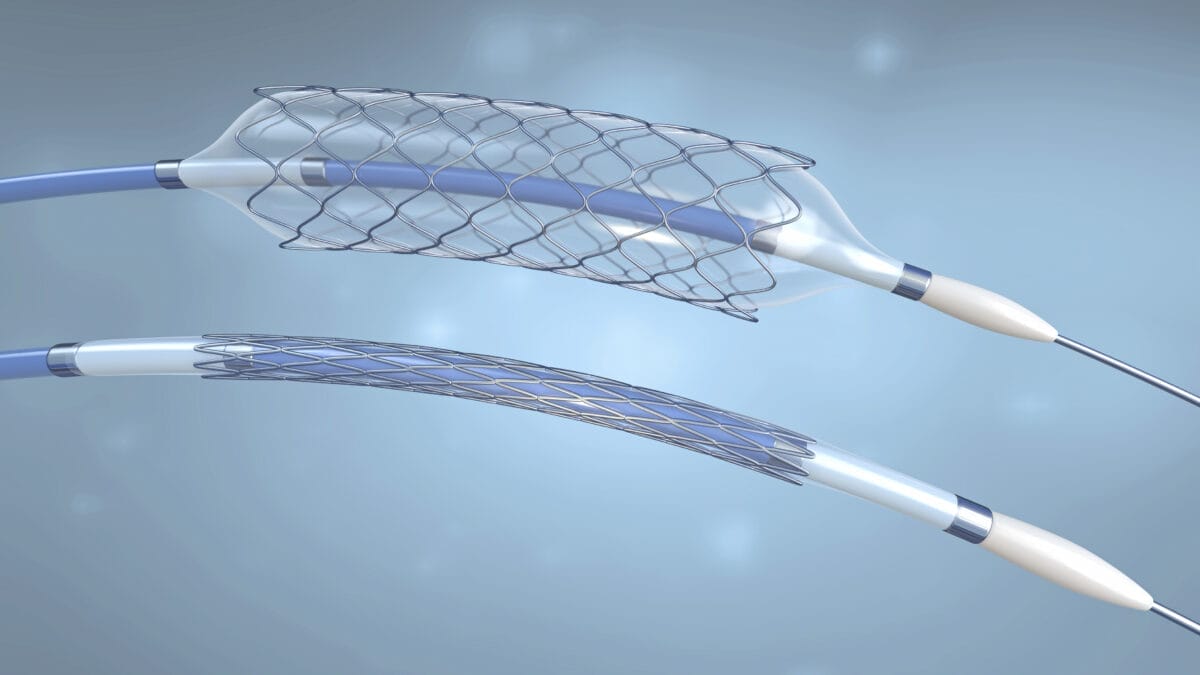
Procedures for melt compounding encompass two kinds of mixing, distributive and dispersive. For example, when fibers are incorporated into a resin, good distribution is required without breaking down the fiber segments: this is characteristic of distributive mixing, a relatively gentle homogenization of the material. Dispersive mixing is associated with the breaking up of agglomerates and generally correlates to high strain and shear rates.
Machines capable of both distributive and dispersive mixing include Banbury-type batch mixers, Farrel continuous mixers, and twin-screw extruders. The twin-screw extruder offers the most flexibility, since the barrel length and screw configurations are adjustable. Downstream oil injection and powder or fiber feeding is also possible.
For materials with good melt strength that are not too soft and tacky, strand pelletizing is preferred. With this method, the pellets are cylinder-shaped and have a diameter of approximately 0.1 in. and a length of 0.125 in. Strand-pelletized compounds feed well on virtually all extruders. Soft and sticky compounds are usually underwater pelletized: the pellets are cut at the die face in a water chamber, conveyed in a pipe with the water, and then separated in a centrifugal dryer. Pellets are typically football shaped or round, with a diameter of 0.1 in. Micro-pellets with diameters as small as 0.02 in. can be produced by underwater pelletization but are generally not recommended for medical compounds because the micro-pellet dies tend to restrict flow and feed rate, causing degradation in sensitive compounds. Small pellets of about 0.06-in. diameter can be produced with a special die that prevents such degradation; these pellets will extrude on the smallest of machines.
Once the need for a new compound is determined, a development team is assembled and the compound requirements are defined. A project plan should include enough time to research existing designs and databases and to determine starting formulations. Acquiring raw materials can necessitate a lead time as long as 2 to 4 weeks. If possible, it is advantageous to schedule compounding time in advance so that materials can be compounded soon after they arrive.
Processing and physical testing come next: several iterations may be required to fine-tune both the formula and the compounding process. When the ingredients are firmly established, biocompatibility testing can begin. Several lots of compound should be produced in order to isolate the effect of control variables such as melt flow and to determine the repeatability and capability of the compounding process.
Once it is verified that the compound meets specified requirements, a production prototype run should be made and final product fabricated. Final validation should include complete biocompatibility testing, physical testing, and field testing. If the validation is successful, a formal specification is written for the compound and a product code assigned.
Today’s catheters are used to diagnose and treat more distal vascular areas, requiring smaller and more precise device components than ever before. Many of these devices must be visible under fluoroscopy to ensure proper placement and navigation during the procedure; yet, plastics used for the construction of these devices are inherently transparent under x-ray. As a result, radiopaque fillers must be blended into the base polymers to provide the necessary visibility or radiopacity.
Foster LoPro® Radiopaque Compounds
Foster LoPro® Radiopaque Compounds include a wide range of the most advanced radiopaque fillers and medical grade polymers to create high quality compounds required for small, ‘low profile’ designs. Medical device manufacturers can work with our team of polymer scientists to custom formulate a blend, tailored to specific application requirements.
Specialty LoPro® Radiopaque Compounds
In addition to the standard LoPro® product line, Foster Corporation has also developed a portfolio of specialty radiopaque materials that were designed with the most critical application requirements in mind.
LoPro Clear™ – Introduced in 2013, LoPro Clear™ is a radiopaque polyurethane that is both x-ray visible and optically transparent. Catheters extruded from LoPro Clear™ can be located inside the body using fluoroscopy while fluid can be visually monitored outside of the body.
LoPro Plus™ – LoPro Plus™ radiopaque compounds are reinforced with nanoparticles for improved pushability of thin-walled catheters. These compounds allow for extrusion of single layer catheters with radiopacity and strength equivalent to conventional bi-layer constructions, in which each layer provides a distinct property.
Common Radiopaque Filler Options
Bismuth Subcarbonate (Bi2O2CO3) offers greater radiopacity that barium sulfate and can be added in smaller volume loadings than barium to achieve comparable results. It is a white powder with high tinting strength, thus limiting color matching in some instances. It is limited by processing temperatures (yellows at 400 F) and in some polymers (not compatible with some thermoplastic polyurethanes).Barium Sulfate (BaSO4) was the first radiopaque filler widely used in medical formulations. It is a relatively inexpensive white powder that has excellent process stability. High loadings are required for comparable radiopacity to other fillers. Because it has poor tinting strength, it is relatively easy to color.
Bismuth Oxychloride (BiOCI) provides excellent radiopacity and is compatible with a wide range of polymers. It is more temperature stable than bismuth subcarbonate. White ‘platelet-like’ particles provide a smooth, pearlescent finish on components. This can provide limitations to exact color matches.
Bismuth Trioxide (Bi2O3) also offers excellent radiopacity in comparably lower loadings and is compatible with most polymers. It is yellow in color and can turn brown at elevated processing temperatures, limiting color matching. Gritty surfaces in finished parts limit use in thin wall and critical surface components.
Tungsten (W) is a very heavy metal powder that is compatible with virtually all polymers at very high loadings by weight. It is dark gray in color and can produce a matte finish in high concentrations, providing substantial restrictions for color matching. Polymer compounds with tungsten can be abrasive on processing equipment. However, it is a filler of choice in very thin walled devices where radiopacity is critical.
Others: Additional radiopaque filler options may be available upon request or by design from our polymer engineering team. Specialty radiopaque fillers, including those used in LoPro Clear™ formulations are proprietary to Foster Corporation.
Market Applications
Interventional Cardiology – Percutaneous Transluminal Coronary Angioplasty (PTCA) devices now reach smaller vascular pathways in and around the heart to deploy balloons that deliver lifesaving stents. Radiopaque compounds provide necessary visibility for physicians navigating these small, thin-walled catheter shafts to the therapeutic region. Tungsten filled polymers replace gold marker bands for substantial visibility and identification of the distal tip.
Interventional Radiology – Small diameter, multi-lumen catheters allow for a wide range of therapeutic applications in radiology. Barium filled polymers, particularly in urethane-based resins (that soften at body temperature), are ideal for peripherally inserted lines and drainage catheters. Increased pushability to more distal vascular regions for angiographic imaging or therapeutic ablation will also benefit from a wide selection of radiopaque formulations using on polyamide polymers with bismuth fillers.
Neurology – Neurological catheters demand excellent mechanical properties to reach distant therapeutic sites as well as sufficient radiopacity for visibility of the small diameter, thin-walled devices. Tungsten filled compounds provide excellent visibility for both diagnostic and therapeutic neurologic catheters. Bismuth filled compounds have also been designed for additional neurological applications such as embolization catheters used to block abnormal blood vessels, most commonly to prevent aneurysms.
Implants – The use of polymers structural devices from spinal cages to dental implants is rapidly expanding. Radiopaque additives allow implanted polymers such as PEEK or polyethylene to remain visible to the physician well after surgery. Foster’s dedicated clean room compounding operations are designed to manufacture radiopaque formulations for implant devices under cGMP conditions.
Documentation:
Lubricity of materials is commonly defined by the Coefficient of Friction (CoF), which is the ratio of force or friction between two bodies and the force pressing them together. The coefficient of friction varies based on materials and environmental conditions such as temperature and moisture. For medical devices, a lower CoF implies better part lubricity and less overall friction between components and contact surfaces.
The CoF can be measured in two different ways: static and dynamic. Static friction refers to objects starting at rest relative to each other, while dynamic (or kinetic), refers to objects that are moving relative to each other. Static friction is usually larger than dynamic for given objects.
Applications Requiring Low Friction
Both molded and extruded medical devices and components often require low coefficient of friction. Medical device applications that require low CoF in dry conditions (i.e. not commonly exposed or immersed in liquids while in use) include handle triggers, buttons and gears. Applications that require lubricity under wet conditions (with blood or fluid contact) are predominantly medical catheters.
Foster ProPell™ Low Friction Polymer Technology
Foster ProPell™ Low Friction Compounds is a platform technology for modifying the surface energy and frictional properties of medical polymers. This surface modification substantially reduces the inherent high friction and tackiness of low durometer polymers commonly used in medical devices, allowing for improved manufacturing and handling.
Foster Corporation’s team evaluates each application and its requirements in order to custom formulate Propell™ technology to meet specific performance demands. Material choice, translucency, color, and post processing steps are all considered to ensure an optimal formulation for each unique project. Though the formulations are custom, all components have been tested and passed USP Chapter 88 Class VI Biological Reactivity studies.
Fluorinated Oils
Perfluoropolyether synthetic oil is colorless, odorless, stable and very inert. It meets USP Class VI biocompatibility and is usually added to plastics in very low loadings (below 5% by weight). Fluorinated oil works well in low durometer thermoplastic elastomer materials for dry applications. Because of the low loading, it allows for bonding to the substrate, which can be a problem for many low friction materials.
PTFE Additives
PTFE powder is perhaps the most common additive for plastics in low friction applications. PTFE is itself one of the most lubricious materials available; however it is not melt processable and, therefore, difficult to form into complex shapes. Small amounts (up to 15%) of PTFE powder can be added to melt processable plastics to improve dynamic frictional properties in medical device applications, performing best under dry conditions. Polymers modified with PTFE additives often maintain good bondability with medical adhesives.
Documentation:
Bacteria and the risk of infection is a significant concern for medical plastic components inserted into the body. Applications of greatest concern are those exposed to bodily fluid for extended periods of time, including but not limited to catheters, wound dressings, hospital bedding, surgical drapes, and hospital gowns.
In terms of medical catheters, the risk of infection is particularly high for those tubes and components that are left in place for three or more days (i.e. in-dwelling catheters). In this case, handling and exposure of these devices can influence time of onset and severity of infection. Infections often occur at incision points, where catheters enter the blood vessel and bacteria is introduced into blood stream.
The general mechanism of infection related to in-dwelling polymers can be summarized as follows: Free floating microorganisms attach to the plastic surface. Colonies of bacteria grow and permanently anchor to plastic surface. A biofilm formation results as colonies grow and mature. Infection occurs when biofilm detaches from plastic substrate.
Foster Antimicrobial Technologies
Foster has developed a range of antimicrobial technologies using both silver and polymer-based solutions, designed to fight infection and prevent the development of bacteria on contact surfaces. Formulations are custom developed to achieve specific application requirements.
Silver ions (a by-product of oxidation) have inherent antimicrobial properties and a history of use in medical applications. These ions attack microbial targets, not only limiting the spread of microbial growth but simultaneously resisting formation. Other materials including carbon and copper, may be added to polymers to tailor oxidation for efficacy and duration.
Agion™ Antiomicrobial Technology – Developed by Sciessent, Agion™ incorporates both silver and copper in a zeolite carrier to fights cell growth by preventing respiration (inhibit transport functions in the cell wall), inhibiting cell division (reproduction), and disrupting cell metabolism.
Foster Combat™ Antimicrobial Master Batches – Foster has designed and developed a line of silver based masterbatches using high loadings of Sciessent Agion™ in a universal polymer matrix. These are dry blended with unmodified polymers at letdown percentages from 2-10%, depending on the polymer and application. These include thermoplastic polyurethane (TPU) used for indwelling catheters, and acrylonitrile butadiene styrene (ABS) and polycarbonate (PC) used for device handles, bedrails and diagnostic equipment housings.
Foster Quaternary Ammonium Compounds – Quaternary Ammonium Compounds are polymer-based antimicrobials that rely on positively charged polyatomic ions to fight infection in medical device applications. These “quats” are blended with polymers to form a permanent bond and retain their ionic charge independent of solution pH. This revolutionary technology offers considerable promise in cost and performance relative to other solutions, particularly silver.
Documentation:
Foster Corporation specializes in custom blending and forming of highly regulated materials, including long-term implantable and bioresorbable polymers. These materials are formulated and processed in a dedicated cGMP cleanroom environment using precise hot melt extrusion. In terms of processing, twin screw extruders offer several advantages for these materials such as easy material feeding, high kneading / dispersing capacities and short transit time. Screw elements, screw rotation and screw speeds can be custom designed for the formulation being produced.
Implantable Polymer Types
Implantable polymers can be categorized based on anticipated duration in the body and range from short-term (<30 days), bioresorbable, long-term (>30 days) to permanent.
Long-Term Implantable Polymers – Long-term implantable polymers include biodurable (non-resorbable) materials such as polyethylene for limited structural applications and polyketones (PEEK) for spinal applications.
Bioresorbable Polymers – Bioresorbable polymers are metabolized by the human body after implantation and include polylactide (PLA), polyglycolide (PGA) and copolymers of PLA/PGA. These materials can be tailored to meet mechanical performance and resorption rates for non-structural drug delivery to resorbable screws and anchors.
Implantable Polymer Additives
Implantable polymers can be enhanced to improve application performance with biomedical additives that provide visibility under x-ray or stimulate bone growth.
Bone Mineral – Phase pure β Tricalcium phosphate (TCP) is an osteoconductive and biocompatible additive that can be melt blended with bioresorbable polymers, such as PLA for the stimulation of bone growth. Alternatively, hydroxyapatite (HA) may also be blended with bioresorbable polymers (PLLA) for biphasic applications including interference screws used in anterior cruciate ligament (ACL) reconstruction.
Radiopaque Fillers – Polymers are inherently transparent to x-ray imaging and require specific additives to achieve visibility. Radiopaque filler selection depends on end application and intended implantation time. For more information, please refer to Radiopaque Compounds.
Documentation:
Colored polymer components provide functionality and aesthetics in medical applications. Colors are used to differentiate product type, size, or model. Certain colors may even convey meaning, such as reds or yellows for warning notification.
Common Coloring Techniques
Colored polymer components can be produced from masterbatch concentrates (blended into natural polymer prior to molding or extruding) or pre-colored polymers via melt blending/compounding. The selection of one coloring method over the other may vary based on economics, secondary operations and end application.
Foster Corporation has processing capabilities to manufacture both masterbatch and pre-colored polymers. Our experienced team of material scientists and process engineers are available to select the most appropriate coloring technique for your requirements.
Pre-Colored Compounds vs. Masterbatches
Masterbatches or color concentrates provide an economical solution for long manufacturing runs of high volume parts. Sufficient setup time is required to ensure the concentrate is properly blended prior to and during the melt processing phase in order to achieve the desired color consistency from part-to-part. This investment may be offset by the economies gained from using a high proportion of unmodified polymer at a reduced price.
The use of masterbatches however, can present several challenges. Metering un-dried masterbatches into hygroscopic resin may impart additional water, which may cause undesirable part appearance, processing and or performance issues. Also, masterbatches require additional handling that may be inconsistent with the natural polymer to which it is added; subsequently resulting in potential production variability. Concentrate pellets are also denser than the natural polymer pellets and tend to sift downward in the hopper, often leading to variable loading levels and color drifts throughout a production run. Although the use of color metering weigh feeders can minimize variation, it also requires additional equipment and production controls. This in turn, reduces the potential cost savings for short production runs.
Pigment Selection
Pre-color compounds and masterbatches can be manufactured using FDA Food Grade Pigments listed under FDA 21 CFR part 173-178 or using FDA Medical Device Pigments listed under FDA 21 CFR Parts 73 and 74. For medical applications, the selection of one pigment classification over the other may affect the FDA approval process.
Documentation:
FDA Medical Device Pigment
Medical compounds require precision feeding, melting and dispersion of polymers and additives to achieve a homogeneous blend. At Foster, all medical compounding is performed on twin screw extruders with processing capabilities suitable for a wide range of base polymers.
Often times in compounding, polymer formulations may require the blending of two commercially available materials to achieve hybrid properties not available from any single resin. Additionally, medical polymers may be blended with specialized additives for enhanced properties to achieve specific functional requirements.
Category | Class | Examples |
---|---|---|
Specialty Polymers | Polyolefins | LDPE, HDPE, LLDPE, PP, EVA |
Styrenics | PS, SAN, ABS, HIPS | |
Vinyls | PVC, PVDC | |
Engineering Polymers | Polyamides | Nylon 6, 6/6, 6/10, 6/12, 11, 12, Amorphous |
Polyesters | PET, PBT, PETG | |
Acetals | Copolymer, Homopolymer | |
Thermoplastic Elastomers | PU, PEBA, COPE | |
Polycarbonate | PCABS | |
Performance Polymers | High Temperature | PEEK, PES, PPS, PSU, LCP |
Fluoropolymers | FEP, PVDF, ETFE |
Melt processible fluoropolymers are a class of thermoplastic polymers where some or all of the hydrogen has been replaced by fluorine. The result is a fully fluorinated polymer or a partially fluorinated polymer.
General Fluoropolymer Advantages
- High temperature performance and endurance
- Outstanding chemical resistance
- High purity
- Excellent UV resistance
- Low friction
- Highly ductile to highly rigid materials
- Opaque to clear materials
- Good fatigue resistance
- Colorable
- Chemically inert
- Excellent flame resistance
- Sterilization
- – EtO – yes
- – Gamma – depends on material
Fluoropolymer Materials (Highly fluorinated)
- FEP
- PFA
- MFA
Fluoropolymer Materials (Partially fluorinated)
- PVDF
- THV
- ETFE
- PCTFE
- ECTFE
Fluoropolymer Additive Options
- Radiopacifiers: Barium sulfate, Bismuth subcarbonate, Bismuth trioxide, Tungsten
- Custom Colors: Pre-colors & concentrates
Foster Fluoropolymer Compounding
At Foster, all fluoropolymer compounds are manufactured using twin screw extrusion processing with corrosion resistant Hastelloy metal coating on all contact surfaces. Multiple down-stream feed ports allow for inputting raw materials at the appropriate stage in the extrusion process. Our range of feeding systems allow for handling pellet or powder ingredients. Programmable screw configurations ensure optimal mixing for both low volume sample development and high-volume manufacturing.
As a leader in polymer compounding for minimally invasive medical devices, Foster has developed a core competency in the custom compounding of thermoplastic elastomers. Thermoplastic elastomers are unique synthetic materials that combine some of the properties of rubber, with the processing advantages of thermoplastics. They consist of a number of families, including:
TPO’S – Polyolefin blends; Ethylene Propylene Diene Modified Rubber (EPDM), Ethylene Propylene Rubber (EPR), Flexible Polyolefin (FPO), Polyolefin Elastomer (POE)
SBC – Styrenic block copolymers; SBS (styrene-butadiene-styrene), SEBS (styrene-ethylene-butylene-styrene) and SIS (styrene-isoprene-styrene)
TPV – Thermoplastic vulcanizate; polyolefin alloys where the rubber portion is fully cured or partially cured
TPU – Thermoplastic polyurethane; polyether or polyester soft block segments coupled to aromatic or aliphatic isocyanate hard blocks
COPE – Copolyester; polyether soft block segments coupled to aromatic polyester hard blocks
PEBA – Polyether block amide and copolyamide elastomers
Like rubbers, the key properties of thermoplastic elastomers are hardness and flexibility. TPEs offer properties bridging the gap between rigid plastics and soft rubbers, like latex or silicone. The families overlap each other in these characteristics. The TPU’S, COPE’S and the PEBA’S offer the hardest and stiffest grades available, because of this they are sometimes referred to as the engineering thermoplastic elastomers.
Medical design engineers are constantly pushing the limits of these TPEs and are always looking for ways to achieve even higher performance than what is currently available. Engineers also want to narrow the specification tolerances, enabling their use in micro-precision molding and thin wall extrusion processes.
Foster ProFlex™ SEBS
ProFlex™ is a comprehensive range of medical grade Styrene Ethylene Butylene Styrene (SEBS) Thermoplastic Elastomers (TPEs) manufactured by Foster Corporation. These unique polymers offer excellent elastomeric properties, with superior design flexibility and ease of processing via injection molding and extrusion. ProFlex® SEBS is available in a range of durometers, with standard formulations, tear resistant and ProPell™ Low Friction formulations also available. Tailored hardness and melt flow properties are also available for custom orders.
ProFlex™ SEBS has passed USP Class VI testing for biocompatibility and is suitable for a variety of medical applications including catheters, surgical handles, ergonomic grips, among other uses.
Documentation:
Since inception, Foster Corporation has focused on the custom formulation and blending of performance materials for critical medical applications. Our range of precision, twin-screw compounding equipment makes Foster ideally suited for custom compounding of high performance thermoplastics, such as Polyetheretherketone (PEEK), Polyetherimide (PEI) and Polyphenylsulfone (PPSU).
Polyetheretherketone
Polyetheretherketone (PEEK) is a semi-crystalline thermoplastic that offers a unique combination of properties including high temperature performance, chemical, hydrolysis and wear resistance, electrical performance, and mechanical properties. The composition and inherent purity result in low levels of ionic extractables, low outgassing, and extremely low smoke and toxic gas emissions. PEEK is highly stable and requires no flame retardant additives to achieve a V-0 rating at 1.45 mm (0.057 in) thickness.
Key Properties of PEEK:
- Maintains properties when exposed to a wide range of temperatures.
- Excellent strength, stiffness, long-term creep and fatigue properties.
- High abrasion and cut through resistance combined with low coefficient of friction.
- Resistant to a wide range of chemicals at elevated temperatures in harsh environments.
- Low moisture absorption, resistant to stream, water and brine, with low permeability.
- Naturally flame retardant with electrical properties which are maintained over a wide frequency and temperature range.
- Inherently pure with low particle generation and low outgassing for reduced contamination.
Polyetherimide
Polyetherimide (PEI) is an amorphous thermoplastic that offers outstanding elevated thermal resistance, high strength and stiffness, and broad chemical resistance. PEI is among the most dimensionally stable thermoplastics available, offering predictability over a wide temperature range. Filled grades offer exceptionally high-tolerance dimensional capabilities. Unlike most other amorphous thermoplastics, PEI resins retain strength and resist stress cracking when exposed to aliphatic hydrocarbons, alcohols, acids, and weak aqueous solutions. Most grades of PEI are inherently flame resistant without additives, exceptionally difficult to ignite, and generate extremely low smoke.
Key Properties of PEI:
- Excellent stability of physical and mechanical properties at elevated temperatures thanks to high glass transition temperature of 217 °C.
- Outstanding strength and amorphous thermoplastic among the available alternatives, with predictable stiffness and strength up to 200 °C.
- Exceptional dimensional stability over a wide temperature range.
- Resistance to aliphatic hydrocarbons, alcohols, acids, and weak aqueous solutions
- Limiting oxygen index (LOI) of 47%, meeting UL94 V0 specifications in sections as thin as 0.41 mm.
- Low smoke generation per the NBS smoke evolution test
Polysulfone
Polysulfone (PSU) is a transparent amorphous thermoplastic that offers higher heat resistance and better hydrolytic stability than polycarbonate (PC). It retains its good mechanical properties when exposed to steam and other sterilization techniques. PSU excels in many fluid-handling applications and has successfully replaced brass in pressurized hot water applications. It exhibits low creep under a sustained load at elevated temperatures and can withstand continuous exposure to hot chlorinated water.
Key Properties of PSU
- HDT of 174°C (345°F)
- High strength
- Good practical toughness
- Excellent hydrolytic stability
- Transparent
- Colorable
Polyphenylsulfone
Polyphenylsulfone (PPSU) is a transparent amorphous thermoplastic that offers the highest performance of the sulfone polymer family, with better impact resistance and chemical resistance than polysulfone (PSU) and polyetherimide (PEI). The high heat resistance and excellent hydrolytic stability of PPSU make it an excellent choice for hot water fittings and medical devices requiring repeated steam sterilization.
Key Properties of PPSU
- High HDT of 207°C (405°F)
- Superior toughness and impact strength
- Exceptional long-term hydrolytic stability
- Better chemical resistance than PSU and PEI
- Withstands over 1,000 cycles of steam sterilization without any significant loss of properties
- Inherently flame retardant
- Transparent
- Colorable
Polyethersulfone
Polyethersulfone (PESU) is a transparent amorphous thermoplastic that combines good chemical resistance with a high heat deflection temperature of 204°C (399°F). This resin is also inherently flame retardant.
Key Properties of PESU:
- HDT of 204°C (399°F)
- Good chemical resistance
- Excellent electrical properties
- Transparent
Foster utilizes a wide variety of specialty additives to enhance specific properties of biomedical polymers. These specialty solutions are custom formulated to meet the unique demands of complex medical devices.
Foster Specialty Polymer Compounds
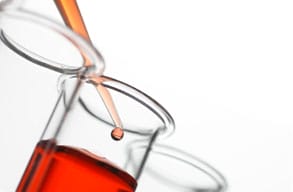
LoPro® – Foster LoPro® Radiopaque Compounds include a wide range of advanced radiopaque fillers and polymers to create high quality compounds that are visible on x-ray or fluoroscopy. For more information on the LoPro® Radiopaque product line see Radiopaque Compounds.
ProPell™ – Foster ProPell™ Low Friction Compounds incorporate proprietary surface enhancing additives into a wide range of medical grade polymers to reduce inherently high coefficient of friction, while retaining desired mechanical properties. For more information on Foster ProPell™ Low Friction Compounds or other lubricious solutions see Lubricious Compounds
PureEase™ – Foster PureEase™ is a range of modified TPU polymers, specifically designed to address common processing concerns and improve consistency and production yields. PureEase™ formulations incorporate very low loadings of processing enhancements into TPU polymers for operational improvements, while maintaining desired mechanical properties. Foster PureEase™ is ideally suited for tube extrusion applications where processing stability and control of ID/OD tolerances are critical.
LazerMed™ – LazerMed™ is a polymer technology that provides a high resolution, permanent and eco-friendly alternative to solvent based printing for medical device applications. LazerMed™ is manufactured using Merck EMD (Darmstadt, Germany) Iriotec™ “state-of-the-art” laser marking pigments to provide a versatile printing platform that can be used in the vast majority of plastic materials.
Nanomed® – Nanomed® compounds are custom formulated to improve structural performance of medical polymers, by incorporating low loadings of clay fillers into the polymer matrix, creating a reinforcing effect. Structural reinforcement is ideal for medical devices and catheters that require a high degree of physician control.
HLS™ – Foster Heat & Light Stabilized Compounds (HLS™) is an stabilizer system that is added at the compounding level to help maintain the integrity of a base resin and extend polymer
shelf life. HLS™ stabilizes polymers by minimizing unanticipated changes in chemistry, molecular weight and color, with exposure to environmental stress agents, such as oxygen, moisture, heat and light.
Fostalink® – Foster offers specialty formulations that process as thermoplastics and are cross-linked post-processing to improve temperature, tensile and durability properties for applications such as heat shrink tubing.
Combat™ – Combat™ is a line of silver-based antimicrobial masterbatches specifically designed to prevent biofilm colonization on medical devices and instruments. For more information see Antimicrobial Formulations.
Hydrophillic Polymers– Hydrophillic additives enhance moisture vapor transmission rate (MVTR) of base polymers to increase breathability
Antioxidants – Antioxidants preserve the chemical and mechanical properties of medical polymers, extending shelf life
Processing Aids – A selection of specialty enhancements to improve dispersion and overall quality of compounded and extruded polymers
Others– Medical polymers can also incorporate additives such as conductive, anti-blocks, minerals, magnetic, among others
Documentation:
LazerMed™ is a polymer technology that provides a high resolution, permanent and eco-friendly alternative to solvent based printing for medical device applications. LazerMed™ is manufactured using Merck EMD (Darmstadt, Germany) Iriotec™ “state-of-the-art” laser marking pigments to provide a versatile printing platform that can be used in the vast majority of plastic materials.
Documentation:
Nanomed® – Nanomed® compounds are custom formulated to improve structural performance of medical polymers, by incorporating low loadings of clay fillers into the polymer matrix, creating a reinforcing effect. Structural reinforcement is ideal for medical devices and catheters that require a high degree of physician control.