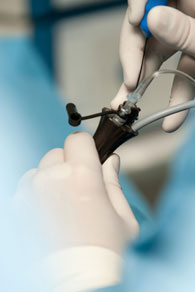
Lubricity of materials is commonly defined by the Coefficient of Friction (CoF), which is the ratio of force or friction between two bodies and the force pressing them together. The coefficient of friction varies based on materials and environmental conditions such as temperature and moisture. For medical devices, a lower CoF implies better part lubricity and less overall friction between components and contact surfaces.
The CoF can be measured in two different ways: static and dynamic. Static friction refers to objects starting at rest relative to each other, while dynamic (or kinetic), refers to objects that are moving relative to each other. Static friction is usually larger than dynamic for given objects.
Applications Requiring Low Friction
Both molded and extruded medical devices and components often require low coefficient of friction. Medical device applications that require low CoF in dry conditions (i.e. not commonly exposed or immersed in liquids while in use) include handle triggers, buttons and gears. Applications that require lubricity under wet conditions (with blood or fluid contact) are predominantly medical catheters.
Foster ProPell™ Low Friction Polymer Technology
Foster ProPell™ Low Friction Compounds is a platform technology for modifying the surface energy and frictional properties of medical polymers. This surface modification substantially reduces the inherent high friction and tackiness of low durometer polymers commonly used in medical devices, allowing for improved manufacturing and handling.
Foster Corporation’s team evaluates each application and its requirements in order to custom formulate Propell™ technology to meet specific performance demands. Material choice, translucency, color, and post processing steps are all considered to ensure an optimal formulation for each unique project. Though the formulations are custom, all components have been tested and passed USP Chapter 88 Class VI Biological Reactivity studies.
Fluorinated Oils
Perfluoropolyether synthetic oil is colorless, odorless, stable and very inert. It meets USP Class VI biocompatibility and is usually added to plastics in very low loadings (below 5% by weight). Fluorinated oil works well in low durometer thermoplastic elastomer materials for dry applications. Because of the low loading, it allows for bonding to the substrate, which can be a problem for many low friction materials.
PTFE Additives
PTFE powder is perhaps the most common additive for plastics in low friction applications. PTFE is itself one of the most lubricious materials available; however it is not melt processable and, therefore, difficult to form into complex shapes. Small amounts (up to 15%) of PTFE powder can be added to melt processable plastics to improve dynamic frictional properties in medical device applications, performing best under dry conditions. Polymers modified with PTFE additives often maintain good bondability with medical adhesives.